Email: [email protected]
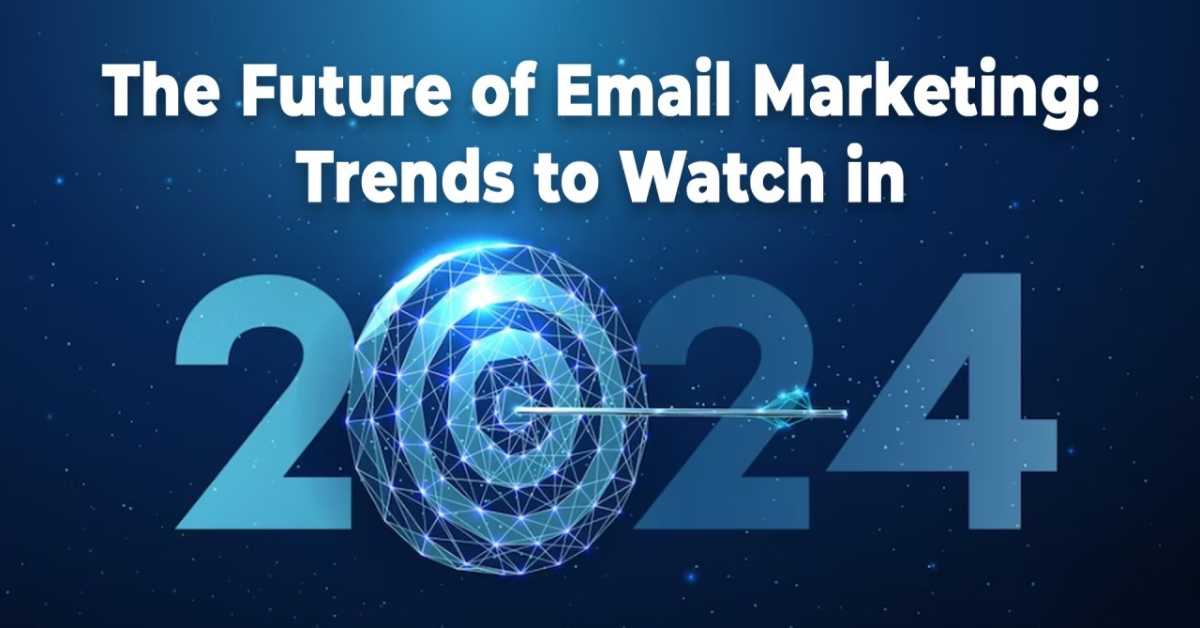
Measuring and improving process efficiency is crucial for businesses to stay competitive and achieve operational excellence in today’s fast-paced and rapidly changing market landscape. By streamlining processes, organizations can enhance productivity, reduce costs, and increase customer satisfaction, ultimately driving business growth and profitability.
Process efficiency directly impacts an organization’s ability to respond quickly to changing market conditions, innovate, and stay ahead of the competition. In this article, we’ll delve into the importance of process efficiency, explore key performance indicators (KPIs) to measure it, and provide actionable tips and strategies to improve it.
We’ll discuss the benefits of process mapping, workflow automation, and continuous improvement methodologies like Lean and Six Sigma. Whether you’re a business leader, operations manager, or process improvement specialist, this article will equip you with the knowledge and tools to optimize your processes, achieve operational excellence, and drive business success.
Process efficiency is vital for businesses to stay competitive and achieve operational excellence. Inefficient processes lead to wasted resources, errors, and delays, resulting in lost revenue, damaged reputation, and decreased customer satisfaction. By improving process efficiency, businesses can enhance productivity, reduce costs, and increase profitability. Effective process management enables organizations to respond quickly to changing market conditions, innovate, and drive growth.
Moreover, process efficiency directly impacts employee morale, engagement, and retention, as streamlined processes reduce frustration and increase job satisfaction. By prioritizing process efficiency, businesses can achieve significant benefits and stay ahead in today’s fast-paced market.
Identifying inefficient processes is a crucial step in optimizing business operations. Start by mapping out your processes using techniques like value stream mapping or swimlane analysis to visualize workflows and identify bottlenecks, unnecessary steps, and areas for improvement. Engage with employees who are directly involved in the processes to gather valuable insights and feedback.
Conduct workshops, surveys, or one-on-one interviews to collect data and gain a deeper understanding of pain points and areas for optimization. Analyze process documentation, workflow diagrams, and performance metrics to identify inefficiencies and opportunities for streamlining. By taking a data-driven approach, you can pinpoint areas for improvement and develop targeted strategies to enhance process efficiency.
Tracking key performance indicators (KPIs) is essential to measure process efficiency and identify areas for improvement. Common metrics include cycle time, throughput, defect rate, and lead time. Cycle time measures the duration of a process, while throughput measures the volume of output. Defect rate tracks errors or defects, and lead time measures the time from initiation to completion.
Additional metrics like process yield, productivity, and capacity utilization can provide a comprehensive view of process efficiency. By monitoring and analyzing these KPIs, businesses can gauge process performance, identify bottlenecks, and implement data-driven improvements to optimize workflows and enhance overall efficiency.
Click on the next page button to continue enjoying the article!
Don’t miss our future updates! Get Subscribed Today!
©2024. Inform. All Rights Reserved.